How do you usually choose an extruder? Not only do you need to analyze your own needs, but you also need to fully understand your suppliers and extruders.
Companies have a basic understanding of whether they need to buy a twin-screw or a single-screw extruder before purchasing a new extruder. What kind of materials need to be produced? Depending on the product specifications, the amount of material used is different. You can refer to "Screw Diameter and Product "Specification size", select the diameter of the screw, and then further select the specifications of the extruder based on the diameter of the screw.
Companies have a basic understanding of whether they need to buy a twin-screw or a single-screw extruder before purchasing a new extruder. What kind of materials need to be produced? Depending on the product specifications, the amount of material used is different. You can refer to "Screw Diameter and Product "Specification size", select the diameter of the screw, and then further select the specifications of the extruder based on the diameter of the screw.
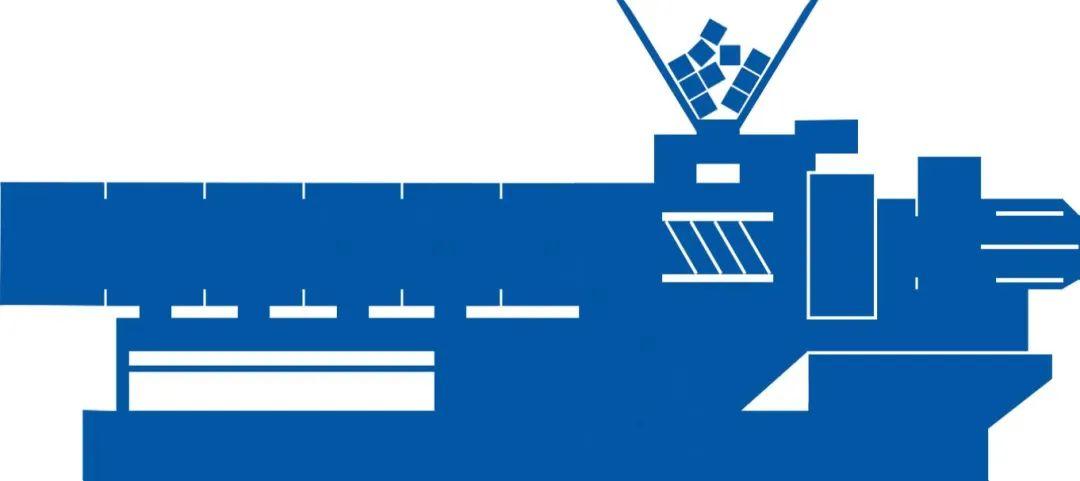
After the type and specification of the extruder are determined, how to find the equipment manufacturer is also an issue that should be paid attention to. Not to mention foreign brands, many domestic extruder companies have been established for a long time, are powerful, and have many years of practical experience. , you can choose from multiple perspectives such as product quality and after-sales service.
Screw speed
This is the critical factor affecting the production capacity of an extruder. The screw speed is not only to increase the extrusion speed and extrusion volume of the material but more importantly, to enable the extruder to achieve high output while achieving good plasticizing effects.
Screw speed
This is the critical factor affecting the production capacity of an extruder. The screw speed is not only to increase the extrusion speed and extrusion volume of the material but more importantly, to enable the extruder to achieve high output while achieving good plasticizing effects.
In the past, the main way to increase the output of extruders was to increase the screw diameter. Although the screw diameter increases, the material extruded per unit time will increase. But an extruder is not a screw conveyor. In addition to extruding materials, the screw also extrudes, stirs, and shears the plastic to plasticize it. Under the premise that the screw speed remains unchanged, the mixing and shearing effect of a screw with a large diameter and a large groove on the material is not as good as that of a screw with a small diameter.
Therefore, modern extruders mainly increase production capacity by increasing the screw speed. The screw speed of an ordinary extruder is 60 to 90 rpm (per minute, the same below) for a traditional extruder. Now it has generally been increased to 100~120 rpm. The higher-speed extruder reaches 150 to 180 rpm.
If the screw diameter remains unchanged and the screw speed is increased, the torque endured by the screw will increase. When the torque reaches a certain level, the screw is in danger of being twisted. However, by improving the material and production process of the screw, rationally designing the screw structure, shortening the length of the feed section, increasing the flow rate of the material, and reducing the extrusion resistance, the torque can be reduced and the screw's bearing capacity can be improved. How to design a reasonable screw and maximize the screw speed under the premise that the screw can withstand it requires professionals to obtain it through a large number of experiments.
Screw structure
The screw structure is the main factor affecting the output of the extruder. Without a reasonable screw structure, simply increasing the screw speed to increase the extrusion volume violates objective laws and will not succeed.
The design of the high-speed and efficient screw is based on high rotational speed. The plasticizing effect of this kind of screw will be worse at a low rotation speed, but the plasticizing effect will gradually improve after the screw rotation speed is increased, and effect will be obtained when the design rotation speed is reached. At this time, both high production capacity and qualified plasticizing effect can be achieved.
Barrel structure
The improvement of the barrel structure mainly involves improving the temperature control of the feed section and setting up a feed chute. The entire length of this independent feeding section is a water jacket, and advanced electronic control devices are used to control the temperature of the water jacket.
Whether the temperature of the water jacket is reasonable is very important for the stable operation of the extruder and efficient extrusion. If the water jacket temperature is too high, the raw material will soften prematurely, and even the surface of the raw material particles will melt, which will weaken the friction between the raw material and the inner wall of the barrel, thus reducing the extrusion thrust and extrusion volume. However, the temperature cannot be too low. A barrel with too low temperature will cause the screw rotation resistance to be too large. When the load-bearing capacity of the motor is exceeded, it will cause difficulty in starting the motor or make the speed unstable. Advanced sensors and control technology are used to monitor and control the extruder water jacket, thereby automatically controlling the water jacket temperature within the process parameter range.
Reducer
Under the premise that the structure is the same, the manufacturing cost of the reducer is roughly proportional to its overall size and weight. Because the shape and weight of the reducer are large, it means that a lot of materials are consumed during manufacturing, and the bearings used are also relatively large, which increases the manufacturing cost.
For extruders with the same screw diameter, high-speed and efficient extruders consume more energy than conventional extruders. It is necessary to double the motor power and increase the frame size of the reducer accordingly. But high screw speed means a low reduction ratio. For reducers of the same size, the gear module with a low reduction ratio is larger than that with a large reduction ratio, and the load-bearing capacity of the reducer is also increased. Therefore, the increase in the volume and weight of the reducer is not linearly proportional to the increase in motor power. If you use the extrusion volume as the denominator and divide it by the weight of the reducer, the number will be smaller for a high-speed and efficient extruder and larger for an ordinary extruder.
In terms of unit output, the motor power of a high-speed and high-efficiency extruder is small and the weight of the reducer is small, which means that the machine manufacturing cost per unit output of a high-speed and high-efficiency extruder is lower than that of an ordinary extruder.
motor driven
For extruders with the same screw diameter, high-speed and efficient extruders consume more energy than conventional extruders, so it is necessary to increase the motor power. A high-speed 65mm extruder needs a motor of 55kW to 75kW. A high-speed 75mm extruder needs a motor of 90 kW to 100 kW. A high-speed 90mm extruder needs a motor of 150 kW to 200 kW. This is one to two times larger than the motor power of ordinary extruders.
During the normal use of the extruder, the motor transmission system and heating and cooling system are always working. The energy consumption of transmission parts such as motors and reduction gearboxes accounts for 77% of the energy consumption of the entire machine; heating and cooling account for 22.8% of the input energy consumption of the entire machine; instrumentation and electrical accounting for 0.8%.
Extruders with the same screw diameter are equipped with larger motors, which seem to consume more electricity. However, in terms of output, high-speed and efficient extruders are more energy-saving than conventional extruders. For example, an ordinary 90mm extruder has a 75kW motor and a production capacity of 180kg. Each kilogram of material extruded consumes 0.42 kilowatt-hours of electricity. A high-speed and efficient 90 extruder has a production capacity of 600 kilograms and a motor of 150 kilowatts. Each kilogram of material extruded consumes only 0.25 kilowatt-hours of electricity. The power consumption per unit of extrusion is only 60% of the former. The energy-saving effect is Remarkable. This only compares the energy consumption of the motor. If the power consumption of the heater and fan on the extruder is taken into account, the difference in energy consumption will be even greater. Extruders with large screw diameters need to be equipped with larger heaters, and the heat dissipation area also increases. Therefore, for two extruders with the same production capacity, the barrel of the new high-speed and high-efficiency extruder is smaller, and the heater consumes less energy than the traditional large-screw extruder, which also saves a lot of electricity in heating.
In terms of heater power, compared with ordinary extruders with the same screw diameter, high-speed and efficient extruders do not increase heater power due to increased production capacity. Because the heater of the extruder consumes electricity, mainly in the preheating stage. During normal production, the heat of material melting is mainly converted by consuming electrical energy from the motor. The conductivity of the heater is very low, and the electricity consumption is not very high. big. This is more obvious in high-speed extruders.
When frequency converter technology was not widely used, traditional large-output extruders generally used DC motors and DC motor controllers. In the past, it was generally believed that DC motors have better power characteristics than AC motors, have a larger speed range, and are more stable when running at low speeds. In addition, high-power frequency converters are relatively expensive, which also limits the application of frequency converters.
In recent years, inverter technology has developed rapidly. Vector-type inverters realize sensorless control of motor speed and torque. The low-frequency characteristics have made great progress, and the price has also dropped relatively quickly. Compared with DC motor controllers, the biggest advantage of frequency converters is energy saving. It makes the energy consumption proportional to the motor load. When the load is heavy, the energy consumption increases, and when the motor load decreases, the energy consumption is automatically reduced. The energy-saving benefits in long-term applications are very significant.
Vibration reduction measures
High-speed extruders are prone to vibration, and excessive vibration is very harmful to the normal use of the equipment and the service life of the machine parts. Therefore, multiple measures must be taken to reduce the vibration of the extruder to increase the service life of the equipment.
The parts of the extruder that are prone to vibration are the motor shaft and the high-speed shaft of the reducer. The high-speed extruder must be equipped with a high-quality motor and reducer to avoid becoming a source of vibration due to the vibration of the motor rotor and the high-speed shaft of the reducer. The second is to design a good transmission system. Paying attention to improving the rigidity, weight, and quality of all aspects of processing and assembly of the frame is also an important step in reducing the vibration of the extruder. A good extruder does not need to be fixed with anchor bolts when in use, and there is no vibration. This depends on the frame having sufficient rigidity and self-weight. In addition, quality control of the processing and assembly of each component must be strengthened. For example, during processing, control the parallelism of the upper and lower planes of the frame, the perpendicularity of the reducer mounting surface and the plane of the frame, etc. During assembly, carefully measure the shaft heights of the motor and reducer, and strictly prepare the reducer pads to make the motor shaft and reducer input shaft concentric. And make the installation surface of the reducer perpendicular to the plane of the frame.
Instrumentation
The extrusion production operation is a black box, and the situation inside cannot be seen at all. It can only be reflected through instruments and meters. Therefore, precision, intelligent, and easy-to-operate instruments will allow us to better understand its internal conditions, so that production can achieve faster and better results.
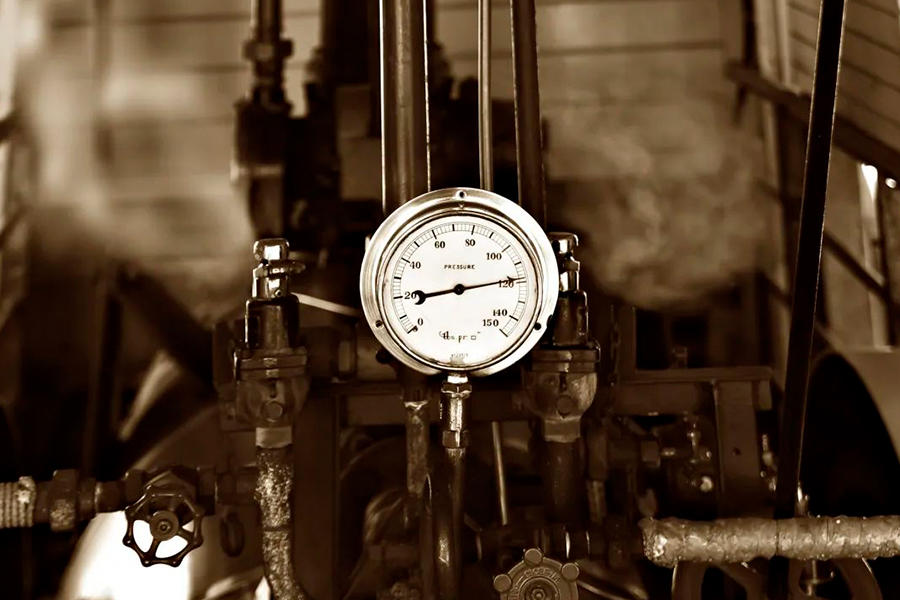
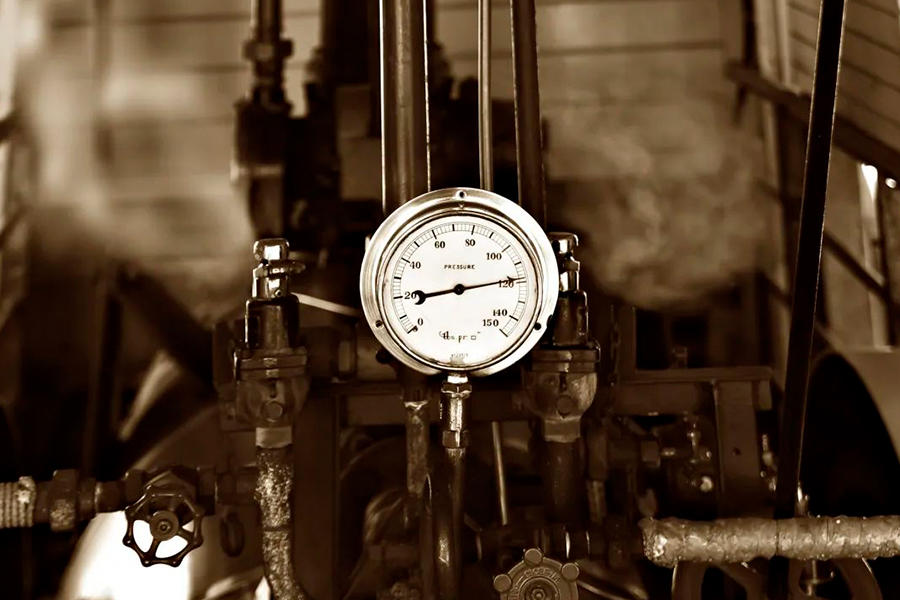